How Nike Laces Get Their Form And Feel
Have you ever stopped to consider the tiny threads that hold your favorite athletic shoes together? It’s almost, that, the shoelaces on your Nike sneakers, while seemingly simple, actually play a rather significant role in how your footwear performs and feels. They are, in a way, much more than just decorative strings; they are a vital component, keeping your foot snug and secure during every stride, every jump, and every casual stroll.
Many folks, you know, might not give much thought to these small, yet mighty, parts of their shoes. Yet, the way they are brought into being, the stuff they are made from, and the careful steps involved in their creation, all contribute to that familiar Nike experience. From the moment the raw fibers arrive, through various transformations, right up to the point they are slipped into a fresh pair of trainers, there's a fascinating sequence of events that unfolds.
So, we're going to take a closer look at the steps involved in bringing these essential shoe fasteners to life. It’s a process that combines material science with precise manufacturing, ensuring that each pair of laces meets the high standards you've come to expect from a brand like Nike. We’ll explore the materials chosen, the techniques used, and how these small items are prepared for their important job.
- Balthazar Wife Viral Video
- That My Line
- Chennedy Carter Gay
- Dog Saying Hi
- Que Pasa Si El Madrid Pierde Hoy
Table of Contents
- What materials are used for how are nike laces made?
- The journey of a fiber: how are nike laces made?
- How do they get their strength: how are nike laces made?
- The braiding process: how are nike laces made?
- What gives them their tips: how are nike laces made?
- Attaching the aglets: how are nike laces made?
- How are Nike laces made to last?
- Quality checks and finishing touches: how are nike laces made?
What materials are used for how are nike laces made?
When thinking about the stuff that goes into making these shoe ties, it’s not just one single thing, you know. Nike, like many companies that produce athletic wear, tends to pick materials that offer a good mix of resilience, a nice feel, and the ability to hold color well. The most common material you'll find for these cords is polyester. Polyester, in fact, is a very popular choice for a good reason. It’s known for its ability to resist stretching, its quick-drying properties, and its general hardiness against everyday wear and tear. This means your shoe fasteners won't easily fray or lose their shape after a few runs or walks.
Sometimes, other materials might be blended in or used for specific types of laces. You might find cotton, which offers a softer feel and a more natural look, though it might not be as resistant to moisture as polyester. Nylon is another possibility, often chosen for its great strength and a bit of elasticity. The selection of the raw material, basically, is the very first step in ensuring the final product can stand up to the demands of active living. It’s about finding that perfect fiber that can be transformed into a reliable, long-lasting part of your shoe.
So, the base ingredient, usually a type of synthetic thread, arrives at the manufacturing facility in large spools. These spools hold countless yards of fine, strong filaments, just waiting to be shaped into the familiar cords we use every day. The consistency and quality of these initial threads are, in a way, absolutely crucial for everything that comes next in the creation process. Without a good starting material, it's pretty hard to make a good finished product, obviously.
- Bald Taylor Swift
- Kendall Jenner Tongue
- Juliette Porter And Clark Drum Still Together
- Ryan Taugher Apology
- Different Strokes For Different Folks Future
The journey of a fiber: how are nike laces made?
Once the raw fibers, typically polyester, arrive at the place where things are made, they don't just magically turn into shoe ties. Their journey begins with a careful preparation stage. First, these fibers need to be unwound from their large spools and, sometimes, given a bit of a twist or a gentle stretch to prepare them for the next step. This initial handling helps to ensure that the individual strands are uniform and ready to be combined with others. It's almost like preparing ingredients before you start cooking; you want everything just right.
Following this, the fibers usually undergo a coloring process. This is where those vibrant hues and classic shades we see on Nike laces come from. The threads are steeped in large vats of dye, allowing the color to deeply penetrate each strand. This method helps the color stay true and prevents it from fading too quickly, even after repeated exposure to sunlight or washing. The choice of dyes and the dyeing process itself are important for achieving consistent color across many batches of laces, which is, you know, pretty important for a brand that values its visual identity.
After being colored, the threads are dried thoroughly. This drying step is quite important to prevent any issues with the material later on, like mildew or uneven texture. They are then wound onto smaller, more manageable bobbins or spools, making them ready for the actual construction phase. This entire initial preparation, in fact, sets the stage for the strength and appearance of the finished shoe fasteners, ensuring they are ready for the intricate processes that will transform them into the final product. It’s a very foundational step, basically, for how are nike laces made.
How do they get their strength: how are nike laces made?
The strength of a shoelace isn't just about the material it's made from; it’s very much about how those individual threads are put together. You know, a single strand of polyester, while strong on its own, wouldn't be nearly enough to hold your shoe on during an intense workout. The true power of a lace comes from the way multiple strands are interwoven or braided. This process distributes the stress across many fibers, making the whole structure far more resilient than its individual parts. It’s a bit like how a rope is made, with many smaller cords twisted together to create something much stronger.
The method of combining these threads is a key factor in determining how durable and flexible the final lace will be. Different patterns of weaving or braiding can give the lace different characteristics, such as how flat or round it appears, how much friction it creates, and how resistant it is to coming undone. So, the design of the lace, in terms of its construction, is just as important as the raw materials themselves for ensuring it can withstand the constant pulling, tying, and untying that a shoelace experiences throughout its life. It's a pretty clever system, actually, that adds significant value.
This careful construction also helps prevent fraying. When threads are tightly bound together, they are less likely to separate or unravel, which extends the lifespan of the lace. A well-constructed lace will maintain its integrity even when subjected to repeated stress, meaning you won't have to worry about it snapping or falling apart when you're in the middle of an activity. The way they build these things is pretty impressive, honestly, and contributes a lot to the overall feel and reliability of your athletic footwear.
The braiding process: how are nike laces made?
The actual formation of the laces usually happens on specialized machines that perform either braiding or weaving. For most Nike laces, especially the common flat or round ones, a braiding process is often employed. Imagine, if you will, many bobbins, each holding a spool of colored thread, arranged in a circular pattern around a central point. These bobbins move in a synchronized dance, passing over and under each other, continuously interlocking their threads. This creates a consistent, uniform cord that slowly emerges from the machine. It’s a fascinating sight, watching all those threads come together, kind of like magic.
The type of braid chosen depends on the desired final product. A "flat braid" involves threads interlocking to create a wide, flat ribbon, which is common for many running shoes. A "round braid," on the other hand, produces a cylindrical cord, often seen on hiking boots or more casual sneakers. The tension applied during this process is very important; it needs to be just right to ensure the lace has the correct firmness and shape. Too loose, and the lace might feel flimsy; too tight, and it could be too stiff to tie comfortably. This precision, you know, is what makes the laces feel consistent from pair to pair.
These braiding machines can operate at a pretty fast pace, churning out many yards of finished lace in a relatively short amount of time. The continuous length of braided cord then moves on to the next stage, which often involves cutting and adding the end pieces. This automated process ensures efficiency and consistency, allowing Nike to produce the vast quantities of laces needed for their footwear. The careful control over this step is a big part of how are nike laces made with such reliable quality.
What gives them their tips: how are nike laces made?
You know those little plastic or metal tips at the end of every shoelace? They have a specific name: aglets. These small additions are actually pretty important. Without them, the ends of your laces would quickly fray and unravel, making it impossible to thread them through eyelets or tie them securely. They give the lace a firm, tidy end, making the process of lacing up your shoes much easier and preserving the life of the lace itself. It’s a very practical design element, basically, that serves a crucial purpose.
The material for aglets is usually a type of plastic, though sometimes metal is used for a more premium look or added durability. The process of attaching them is quite precise. The raw, braided cord, after being cut to the correct length, is fed into a machine that forms and secures these tips. This machine takes a small piece of the chosen material, wraps it tightly around the end of the lace, and then typically uses heat or a strong adhesive to bond it permanently in place. This creates that smooth, sealed tip that slides easily through shoe eyelets.
The quality of the aglet attachment is, in a way, a good indicator of the overall quality of the lace. A poorly attached aglet can come off easily, leaving you with a frayed end and a frustrating experience. Nike, like other reputable brands, pays close attention to this detail, ensuring that the aglets are firmly secured and durable enough to withstand repeated use. It's a small detail, but one that makes a big difference in the user experience and the longevity of the product. So, the little tips are actually a pretty important part of how are nike laces made.
Attaching the aglets: how are nike laces made?
The process of putting the aglets on the ends of the laces is typically an automated one, following the braiding and cutting of the main cord. Once the long braided ropes are produced, they are fed into a cutting machine that precisely measures and snips them into the specific lengths required for different shoe sizes and styles. Immediately after cutting, these individual lace segments move along a conveyor system to the aglet application station. This is where the magic happens, so to speak, turning a simple cut cord into a finished shoelace.
At the aglet station, small pieces of plastic film, pre-cut to the right size, are positioned around the freshly cut ends of each lace. A specialized machine then wraps this film tightly around the lace end. Heat is often applied at this stage, causing the plastic to soften and fuse around the fibers of the lace, creating a strong, permanent bond. Sometimes, a high-frequency vibration or a strong adhesive might be used instead of heat, depending on the specific materials and desired finish. The goal, however, remains the same: to create a robust, sealed tip that won't come off easily. It's a very quick and efficient process, allowing for high-volume production.
The machines are calibrated to ensure consistent pressure and temperature, guaranteeing that each aglet is applied with the same strength and precision. This attention to detail means that the tips are not only secure but also uniformly shaped, which helps them slide smoothly through the eyelets of the shoes. The final appearance of the aglet is also important; it needs to be neat and free of rough edges. This entire step is a vital part of the finishing process, making sure that when you get your new pair of shoes, the laces are ready for immediate use and will hold up over time. This stage is, basically, the last major manufacturing step in how are nike laces made.
How are Nike laces made to last?
The durability of Nike laces isn't just a happy accident; it’s a direct result of careful material selection, precise manufacturing techniques, and, importantly, a series of quality checks throughout the production line. To make sure these shoe fasteners stand up to the rigors of athletic activity and daily life, they are designed with longevity in mind from the very start. The choice of strong, resilient fibers like polyester, as we discussed, is the foundational element. These materials inherently resist abrasion, stretching, and damage from moisture, which are common causes of lace failure.
Beyond the raw materials, the way the laces are constructed plays a huge role in their lifespan. The tight braiding patterns ensure that the individual threads are securely interlocked, preventing them from unraveling or fraying easily. This dense construction also gives the laces a certain amount of resistance to snagging or tearing. Think about how much tension a lace undergoes when you pull it tight or tie a double knot; the robust braiding allows it to absorb this stress without breaking down. It's almost, that, every part of the making process is geared towards enduring use.
Furthermore, the dyeing process is also important for durability. High-quality dyes that are properly applied mean the color won't bleed or fade quickly, which can sometimes weaken the fibers over time. And, of course, the secure attachment of the aglets is absolutely critical. A lace that frays at the ends quickly becomes unusable, regardless of how strong the main body is. So, the combination of superior materials, expert braiding, and reliable finishing touches all contribute to the overall resilience and long life of these essential shoe components. It’s a very comprehensive approach to ensuring lasting quality.
Quality checks and finishing touches: how are nike laces made?
Even after all the braiding, cutting, and aglet application, the process isn't quite finished. Before these laces make their way to a shoe factory, they undergo a series of quality checks. These inspections are pretty important to make sure that every lace meets Nike’s standards for appearance, strength, and overall function. Workers or automated systems will examine the laces for any imperfections, such as uneven braiding, stray threads, or poorly attached aglets. They might also check the length to ensure consistency, as a lace that’s too short or too long can affect the fit of a shoe. It’s a bit like a final exam for the laces, you know, before they get their diploma.
Beyond visual inspection, some laces might undergo more rigorous testing. This could involve pulling them with a certain amount of force to check their tensile strength, or subjecting them to repeated bending to see how well they resist fatigue. These tests simulate the real-world stresses that laces experience, helping to confirm that they will hold up during actual use. This attention to detail at the end of the production line is a crucial step in maintaining the brand's reputation for reliable products. It ensures that when you get a pair of Nike shoes, the laces inside will perform as expected, every single time.
Once they pass all the checks, the laces are typically bundled or spooled in preparation for shipping to the various shoe assembly plants around the world. Sometimes, they might be treated with a special coating to enhance their water resistance or to give them a particular feel. This final preparation ensures they arrive at the shoe factory in perfect condition, ready to be integrated into the finished footwear. This whole process, from the very first fiber to the final inspection, is what ensures that the shoe fasteners you find in your Nike sneakers are reliable, good-looking, and ready for whatever activity you throw at them. So, in some respects, the care taken here is what makes all the difference in how are nike laces made.
The creation of Nike laces involves selecting resilient materials like polyester, carefully dyeing them for lasting color, and then using precise braiding techniques to give them strength and shape. The process includes accurately cutting the cords and securely attaching aglets to prevent fraying, followed by thorough quality checks to ensure each lace meets performance and appearance standards.
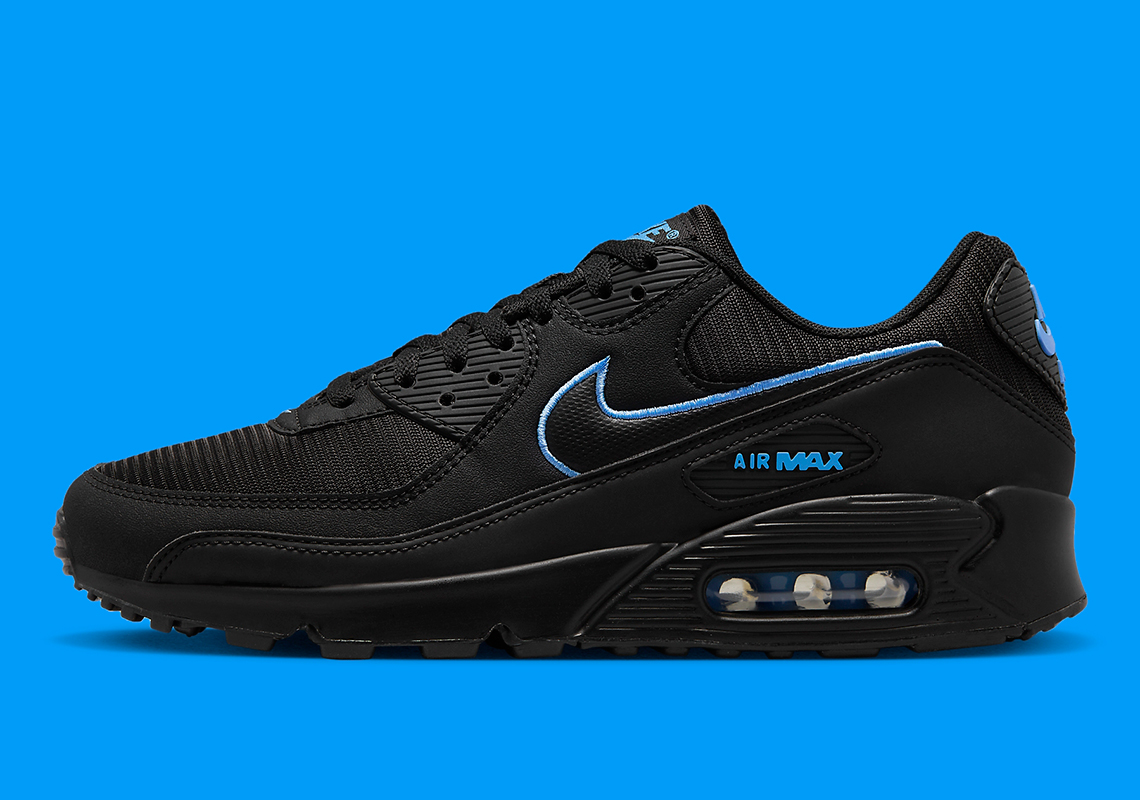
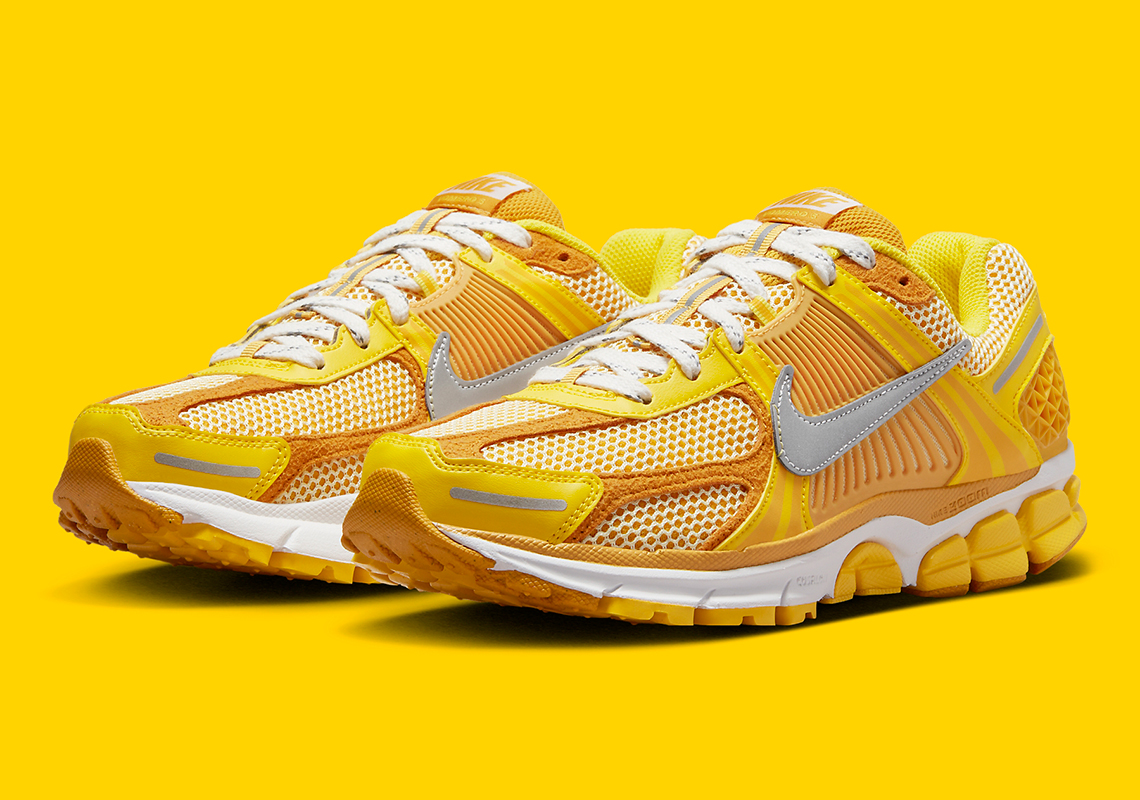
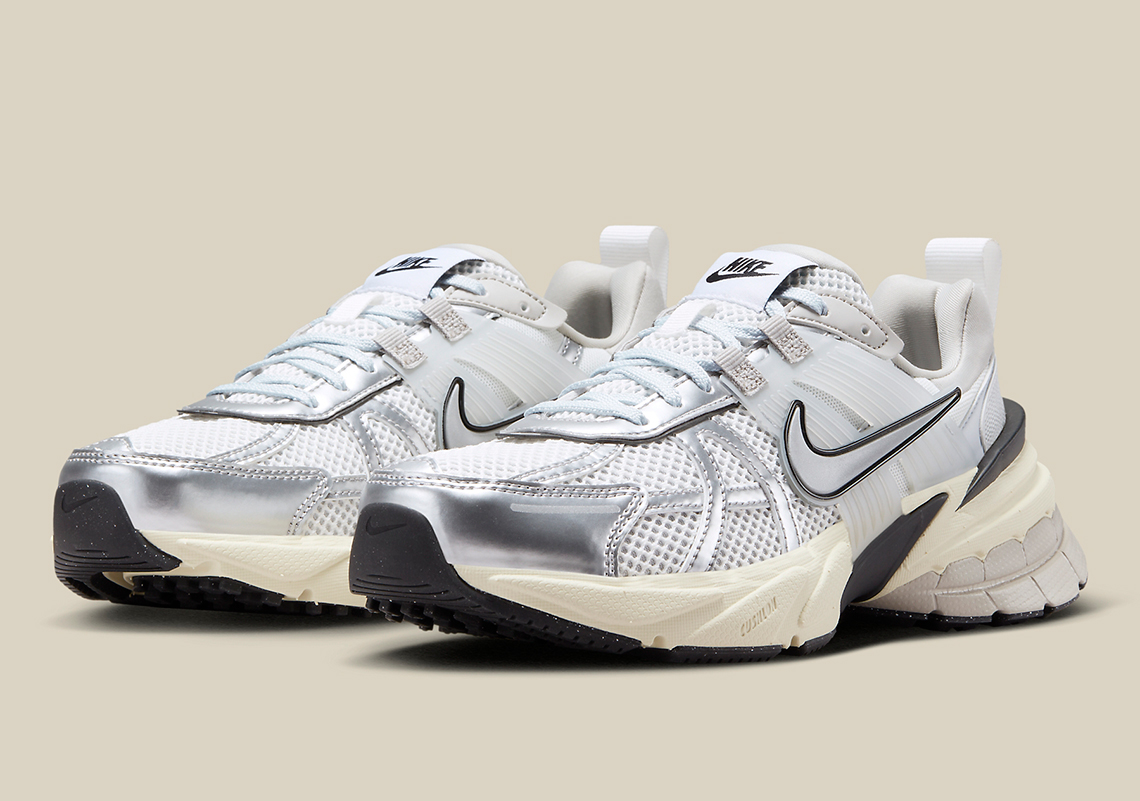
Detail Author:
- Name : Albina Conn
- Username : trantow.porter
- Email : schaefer.sigurd@kunze.org
- Birthdate : 1994-08-01
- Address : 1236 Eleanore Court East Ludwigside, HI 63408
- Phone : 541-712-0897
- Company : Powlowski, Bode and Dickinson
- Job : Tool and Die Maker
- Bio : Culpa iusto et distinctio et architecto. Non quam quod earum in sunt. Aliquid rerum dolorem est. Architecto unde et est impedit excepturi.
Socials
linkedin:
- url : https://linkedin.com/in/kip_goyette
- username : kip_goyette
- bio : Et accusamus atque est et natus.
- followers : 6936
- following : 2700
twitter:
- url : https://twitter.com/kipgoyette
- username : kipgoyette
- bio : Voluptatibus molestiae id veritatis sint vel. Aut unde asperiores quo est. Itaque quo exercitationem earum nulla at dolorem.
- followers : 4674
- following : 27
instagram:
- url : https://instagram.com/kip.goyette
- username : kip.goyette
- bio : Et corrupti et blanditiis facere. Nesciunt quo aspernatur consectetur necessitatibus.
- followers : 3493
- following : 2060
facebook:
- url : https://facebook.com/kgoyette
- username : kgoyette
- bio : Error ipsa nihil quos iure nesciunt omnis.
- followers : 5588
- following : 578
tiktok:
- url : https://tiktok.com/@kip_goyette
- username : kip_goyette
- bio : Quis maiores omnis et libero. Dolore et excepturi enim veniam eum.
- followers : 4225
- following : 605